Investigation summary
What happened
On 2 August 2024, a Leonardo Helicopters AW139, registered VH‑EXK, departed Longford Heliport, Victoria, for a hoist training exercise conducted under visual flight rules near Golden Beach, Victoria. During the training, the crew faced difficulties retrieving a waterborne training aid, but due to encroaching fog the instructor (Pilot Flying) elected to depart for Longford. They initiated a climb with the aid of the radar height hold function before ensuring the helicopter was correctly configured for departure. The helicopter then inadvertently entered instrument meteorological conditions (IMC) and the altitude and airspeed began to fluctuate. The enhanced ground proximity warning system then triggered as a result of increased airspeed and the helicopter’s flight path descending below 150 ft above sea level. The captain (Pilot Monitoring) took control and initiated a climb, allowing for a safe return to Longford Heliport without further incident.
What the ATSB found
Due to encountering fog the instructor conducted a hastened departure from the training area before securing the hoist, the cabin door and occupants. At the time, the captain, who was acting as pilot monitoring, was still occupied with recording the training aid position. During the initial climb, the helicopter inadvertently entered the encroaching fog, and the instructor, who was the pilot flying, lost visual references and became spatially disoriented.
The disoriented instructor attempted to exit instrument meteorological conditions but applied control inputs that resulted in the helicopter entering an unstable state. This triggered a terrain alert, and airspeed exceedances with the main rotor RPM at 102% and operations with the door open and the hoist extended.
Following the terrain warning, the captain took control of the helicopter prior to gaining situational awareness or conducting an appropriate control handover, increasing the risk of control conflict between the 2 crew members. Additionally, the operator had no defined procedures for inadvertent instrument meteorological conditions recovery during hoist operations or for responding to enhanced ground proximity warning system alerts and advisories.
Despite not gaining situational awareness and bypassing handover protocols, the captain’s control inputs immediately arrested vertical descent and initiated a climb, reducing the risk of collision with terrain.
What has been done as a result
Following this incident, Esso Australia conducted an internal investigation and has identified several actions to be taken.
- A standardised procedure has been developed to ensure a controlled entry into instrument meteorological conditions from a low hover, including scenarios where aircrew may be connected to the hoist beneath the aircraft.
- Flight crews will undergo further training during low-level operations in the helicopter and simulator to reinforce techniques for handling degraded visual environments.
- Briefings for search and rescue and hoisting training operations will emphasise the importance of maintaining a safe distance from visibility-reducing conditions.
- Crew resource management courses will also be updated to focus on upset training scenarios and flight crew responses.
Safety message
The ATSB encourages pilots to take proactive measures to manage the risks associated with inadvertent entry into instrument meteorological conditions. Loss of visual references can lead to spatial disorientation, reduced situational awareness and loss of control, particularly for pilots operating under visual flight rules. Pilots rated for instrument flight rules should prioritise the use of rehearsed recovery procedures, referencing flight instruments to safely regain visual meteorological conditions.
This incident shows the importance of establishing and monitoring operational safety margins, adherence to documented procedures, maintaining situational awareness and fostering effective crew resource management during high-workload scenarios like hoisting and search and rescue operations. The challenges presented by degraded visual environments, such as inadvertent entry to instrument meteorological conditions, increase the likelihood of spatial disorientation and loss of control in flight.
These proactive steps can significantly enhance safety and improve outcomes during low‑level operations in demanding conditions.
The occurrence
On 2 August 2024, a Leonardo Helicopters AW139, registered VH-EXK and operated by Esso Australia, departed Longford Heliport, Victoria at 0816 local time for a hoisting training exercise. The crew consisted of the captain, a flight instructor, a check aircrewman, and a hoist operator. The captain was initially the pilot flying (PF)[1] and was under the supervision of the instructor who was acting as pilot monitoring (PM).[2] The hoisting exercise took place near Golden Beach, Victoria (Figure 1) and was conducted under visual flight rules (VFR).[3] The crew crossed the coastline at 0821 and selected a training area approximately 2 km offshore. The exercise involved retrieving a training aid amidst large swells, sea spray and encroaching fog from the north-west. The training aid was deployed, and the exercise commenced at about 0825.
Figure 1: EXK track and key locations
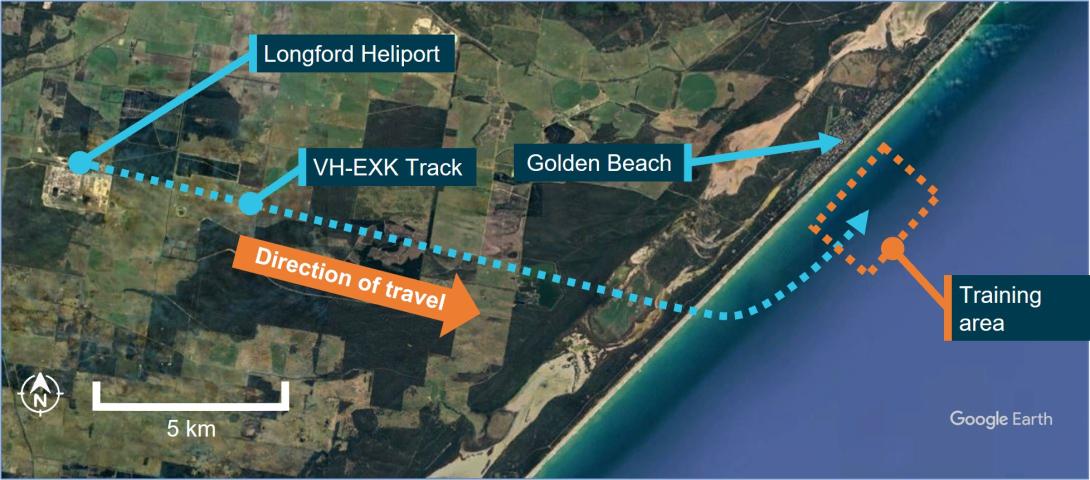
Source: Google Earth, annotated by the ATSB
As the training progressed, the helicopter's proximity to the fog on the left side, where the instructor was seated, was observed to be decreasing. The flight crew noted that the skies were clear to the north and northeast of their position on the instructor’s side of the helicopter.
After conducting training for approximately 40 minutes, the instructor assumed control as PF and the check aircrewman assumed the role of hoist operator to retrieve the training aid. This involved hovering in a stationary position approximately 40 ft above the water's surface to retrieve a training aid, which was a wooden cross with ropes attached, designed to simulate a search and rescue scenario.
However, the attempt was unsuccessful, and due to the encroaching fog, the instructor immediately elected to depart and announced they would climb to avoid fog.
At 0908, the instructor manoeuvred the helicopter onto a north-westerly heading (Figure 2) and engaged the radar height hold (RHT) system while climbing using a combination of the collective[4] beep trim and force trim release (FTR).[5] At this time, the captain, acting as the PM, was focused on marking the GPS position of the training aid. This facilitated its retrieval in a subsequent training exercise later that day, as the large swells and fog disrupted the current exercise. During the departure climb, the right cabin door was open and approximately 40 ft of the hoist cable was extended.
Figure 2: EXK flight track and enhanced ground proximity warning system alert
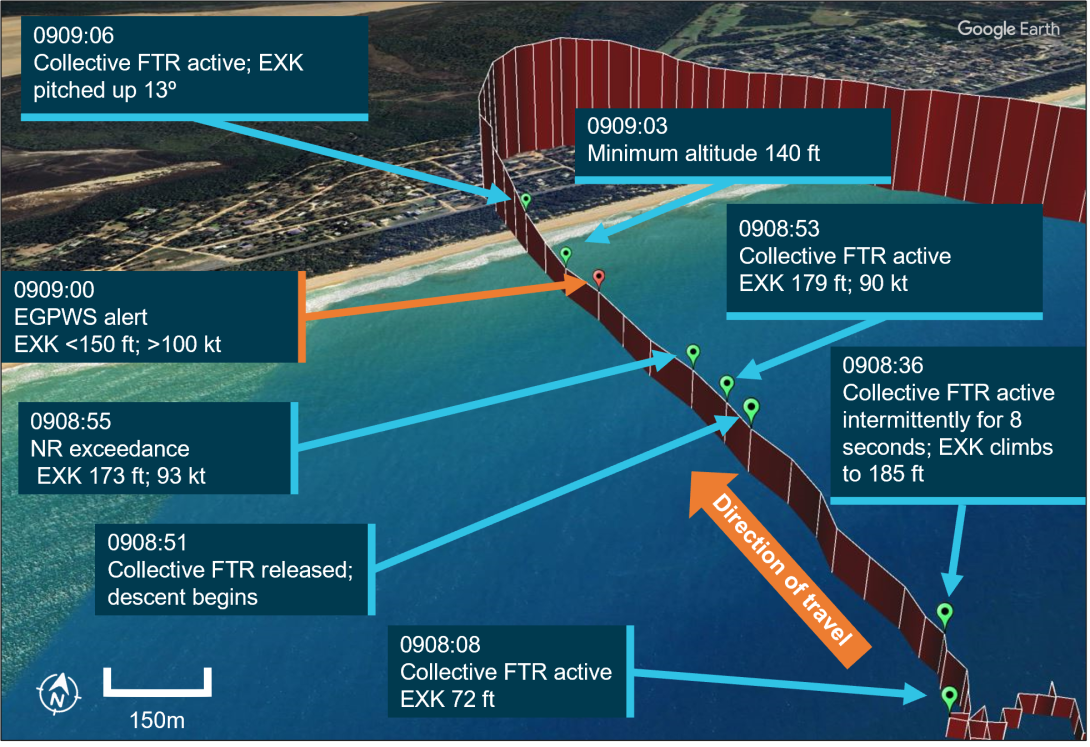
Source: Google Earth, annotated by the ATSB
At about this time, the helicopter inadvertently entered instrument meteorological conditions (IMC),[6] and the instructor announced their intention to move forward to depart. The check aircrewman objected via the intercom to departing with the hoist still extended, as the post‑hoist procedures requiring the aircrew to secure the hoist cable and cabin had not yet been completed. Despite their objection, the instructor proceeded with the departure to regain visual meteorological conditions (VMC).
The instructor accelerated and continued to climb, reaching an altitude of 185 ft and an airspeed of 72 kt before beginning a shallow descent. The instructor who was PF noticed the increasing airspeed but took no actions to arrest this trend. As the helicopter continued accelerating, the captain observed on the primary flight display (PFD) a nose-down attitude and airspeed increasing through 80 kt, which exceeded the operational speed for the hoist operation. The captain announced ‘80 kt’ to draw the attention of the instructor to the increasing airspeed. The airspeed continued to increase above 90 kt, which resulted in an airspeed exceedance with the RPM (NR) at 102%, despite the captain’s attempt to set the RPM switch[7] to 100% to avoid this exceedance. As the helicopter accelerated through 100 kt it exceeded the maximum airspeed for the right main cabin door in the open and locked position.
At 0909, the helicopter had descended to 147 ft above sea level with an airspeed of 101 kt, triggering caution and warning alerts from the enhanced ground proximity warning system (EGPWS). In the 10-second period preceding the EGPWS warning, the collective FTR was active for 5 seconds while it was engaged and disengaged 3 times. The instructor recalled climbing and using the collective beep trim and collective FTR. However, they did not recall engaging the collective FTR after the negative vertical speed developed. The captain later noted that the collective FTR could be activated instinctively while manipulating the collective due to the switch's position, requiring discipline to avoid unintentional activation.
Responding to the increasing speed and ground proximity alert on the PFD, the captain reactively assumed control, reduced the helicopter’s speed, and initiated a climb by pulling back on the cyclic.[8] The check aircrewman suggested cutting the hoist cable for safety and indicated that the cable was trailing behind the aircraft. This was not actioned after consultation with the instructor, who stated they were satisfied that the cable did not pose a danger, and they lacked visual reference to the ground. The instructor decided not to cut the cable because they were unsure of what was underneath the helicopter at the time.
During the recovery, the captain climbed on a north‑westerly heading and reduced the helicopter’s airspeed and the instructor resumed control after a brief exchange with the captain. The flight crew regained VMC shortly after the recovery was initiated, recovered the cable and the helicopter was flown in an easterly direction away from the shoreline. The crew configured the helicopter for departure from the training area and returned to Longford Heliport. The helicopter landed without further incident at 0936 local time.
Context
Pilot information
Instructor
The instructor held an Airline Transport Pilot Licence (helicopter) with an instrument rating and a Class 1 aviation medical certificate. They had 11,129 flight hours, including 3,695 hours on the AW139, they had also logged 114 hours on the AW139 in the last 90 days. They were approved for training and checking duties with the operator, Esso Australia, including hoisting operational proficiency checks.
The instructor reported sleeping 7 hours the night before the occurrence. They were awake for 4 hours and were on duty for 2 and a half hours at the time of the occurrence, they stated they felt ‘alert but not at peak performance’.
Captain
The captain held an Airline Transport Pilot Licence (helicopter) with an instrument rating and a Class 1 aviation medical certificate. They had 15,402 flight hours, including 2,603 hours on the AW139 and had logged 81.9 hours on the AW139 in the last 90 days. They were approved as a line supervisory pilot with the operator.
The captain reported sleeping 7 and a half hours the night before the occurrence. They were awake for 4 hours and were on duty for 2 and a half hours at the time of the occurrence. They reported feeling ‘somewhat fresh’.
Helicopter information
The Leonardo Helicopters AW139, serial number 31886, was registered as VH-EXK in Australia to the operator, Esso Australia, on 8 January 2020. The helicopter was certified for day and night VFR, IFR,[9] offshore/elevated helideck[10] operations, and external load[11] operations.
Powerplant
The AW139 is equipped with two Pratt & Whitney PT6C‑67C engines. The main rotor power can be set to 100% or 102% using the RPM selector switch (Figure 3) on the pilot’s (right seat) collective grip.
For Category A[12] operations below 80 kt, rotor RPM (NR) is set to 102%, enabling optimal performance in the event of an engine failure, allowing for either continued safe flight or a controlled landing. Real‑time rotor RPM is monitored on the multi‑function display with the maximum airspeed set to 90 kt at 102% NR to protect the rotor system from excessive stress.
Crew alerting system (CAS) messages are not triggered during RPM adjustments, allowing for changes without distracting alerts.
Figure 3: Pilot RPM selector switch
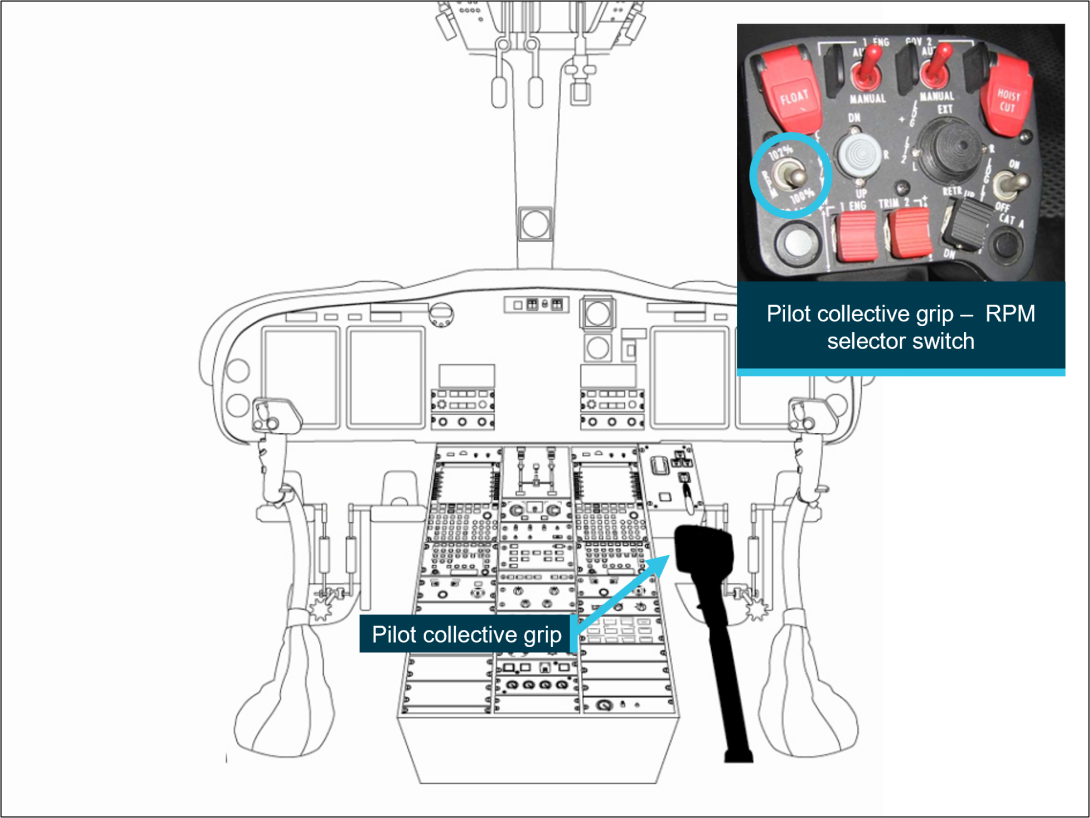
Source: Leonardo Helicopter file photo, annotated by the ATSB
Autopilot and radar height hold
The AW139 is fitted with a 4‑axis autopilot system coupled with a 3‑cue flight director (FD), which controls the helicopter’s pitch, roll, yaw, and vertical axis. The radar height hold (RHT) mode maintains the helicopter at the radar height at the time of engagement. The RHT reference height is presented on a magenta bug (Figure 4) on the radar altimeter tape with a digital readout.
The helicopter flight manual stated that during hoist operations, that pilots should consider the effect of the use of the RHT function in flight and to monitor the helicopter performance closely when used.
Figure 4: RHT reference height
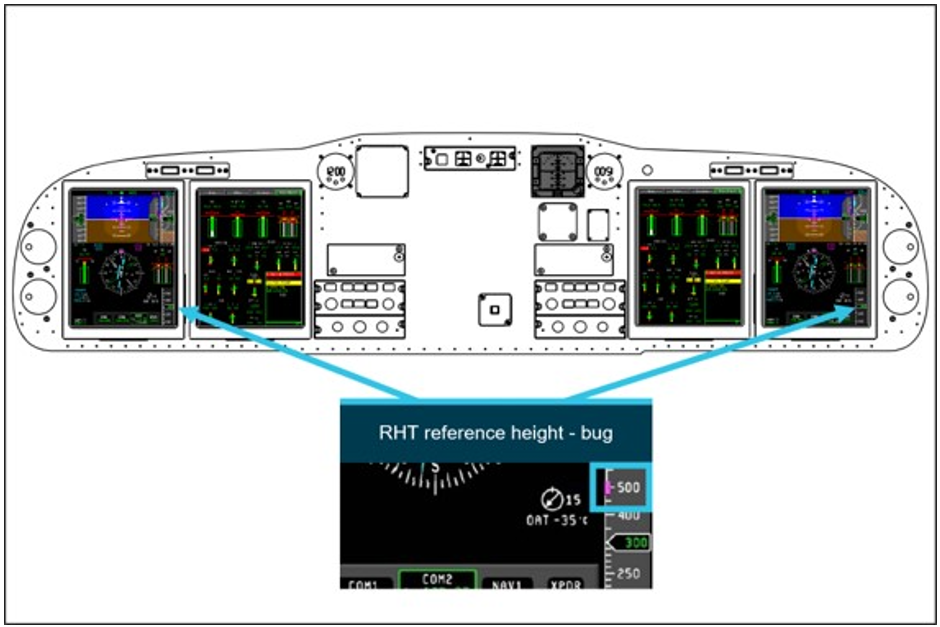
Source: Operator, annotated by the ATSB
The RHT reference height is adjustable using the following methods:
- Collective force trim release (FTR): the ‘push and hold’ collective lever trim release button (Figure 5 left insert) is depressed to disengage the spring feel mechanism which enables the collective to be moved freely. When the button is released, the spring feel[13] is reset to zero force and the reference height is reset.
- Collective beep trim switch: crews make incremental height adjustments using the collective beep trim switch, moving it aft to increase height and forward to decrease it (Figure 5 right insert). Adjustments occur at a rate of ±50 ft/second down or up, with audio tones (beep) signalling changes.
While RHT is designed to assist in stable altitude hold, crews are required to actively monitor and control the flight path.
Figure 5: Crew collective grips, collective FTR button and collective beep switch
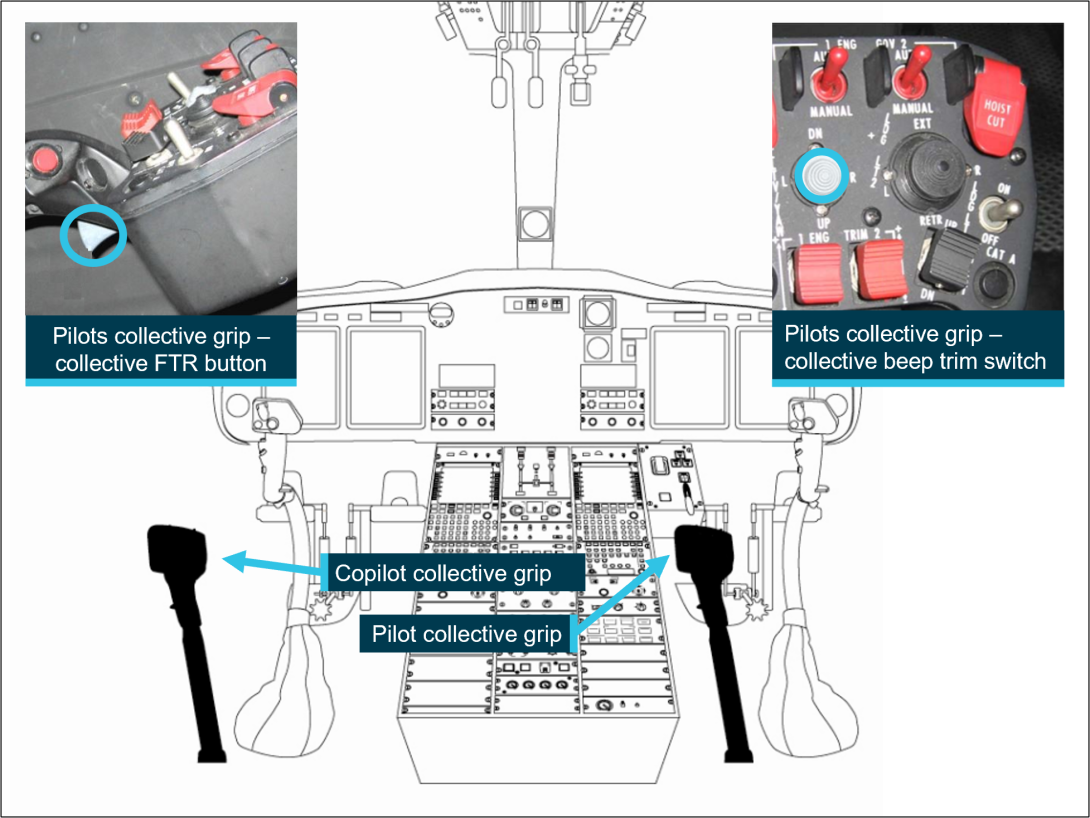
Source: Leonardo Helicopters file photos, annotated by the ATSB
Cabin doors and hoist system
The sliding cabin doors fitted to VH‑EXK allowed for in‑flight hoisting operations, with speed limitations in place to prevent damage from slipstream pressure. The door could be locked open during hoist use. The operator required that the airspeed not exceed 80 kt when opening or closing the cabin sliding door and 100 kt when the door was locked open. The helicopter’s hoist system, located on the right side of the cabin, was equipped with an electric hoist motor, winch, and safety features including the primary quick release system, accessible to both flight crew and the hoist operator.
Enhanced ground proximity warning system
The helicopter was equipped with a Honeywell MK XXII‑30 enhanced ground proximity warning system (EGPWS), which displays terrain and obstacles. It is designed to provide alerts about nearby terrain or obstacles approximately 30 seconds ahead of the aircraft, giving warning of potential conflicts.
The functionality of the terrain awareness display and the ‘look ahead’ alerting and warning function was detailed in the AW139 rotor flight manual as:
This function uses information from the GPS and other sources on the aircraft to calculate horizontal position and vertical altitude. This data provides a three-dimensional position for the aircraft. This position is then compared to the terrain database and if a conflict with terrain or a known obstacle is imminent the system provides an alert.
Offshore mode
The EGPWS system fitted to the operator’s AW139 fleet included a dedicated offshore mode, which could be activated by the flight crew. Offshore mode is recommended for operations over water, as it adjusts terrain awareness boundaries to minimise nuisance alerts. This mode inhibits certain alerts and warnings in specific flight conditions. However, offshore mode is unsuitable for conventional IFR procedures, as it modifies terrain alerting parameters essential for standard instrument approaches and departures.
Operator information
Esso Australia operated from its headquarters in Longford, Victoria, supporting gas platform operations in Bass Strait. On 11 June 2024, the operator was issued with an air operator’s certificate (AOC), authorising Australian air transport operations and a Part 138 aerial work certificate, authorising aerial work operations.
Esso Australia operated a single helicopter type, the Leonardo AW139 helicopter, primarily for passenger transport, cargo transport and specialist aerial work operations, including external load and dispensing tasks. Its personnel were authorised to conduct both VFR and IFR flights.
Meteorological information
On the morning of 2 August 2024, the flight crew stated they conducted a weather briefing at the Esso Australia heliport base in Longford, Victoria. They recalled the presence of fog which delayed the departure by about an hour. While the crew prepared for departure, they received a report from another Esso Australia helicopter crew that the fog had sufficiently dissipated in the aera. Following a routine job safety analysis (JSA)[14] and final weather review, the crew assessed that the remaining fog posed no significant concern and proceeded with the flight.
Graphical area forecast
The flight to the training area and back was within the graphical area forecast for Victoria (GAF VIC), covering subdivisions A and A1. For the duration of the flight, the forecast conditions indicated:
- visibility greater than 10 km, with broken stratus clouds between 100 and 1,000 ft above mean sea level (AMSL) in A1.
- isolated freezing fog over land, with scattered fog south‑east of Mangalore and Wangaratta airports, reducing visibility to as low as 300 m.
Terminal forecast and special weather report East Sale (YMES)
The terminal forecast for East Sale predicted calm winds from 320° at 3 kt, with visibility reduced to 200 m in freezing fog, early in the morning.
By 0930 local time, conditions were expected to improve to greater than 10 km visibility with light winds. A 30% chance of mist, reducing visibility to 1,000 m was also forecast between 0900 and 1000. A special report (SPECI) at 0800 recorded calm conditions, with freezing fog reducing visibility to 200 m with scattered clouds at 100 ft.
Figure 6: Weather reporting locations
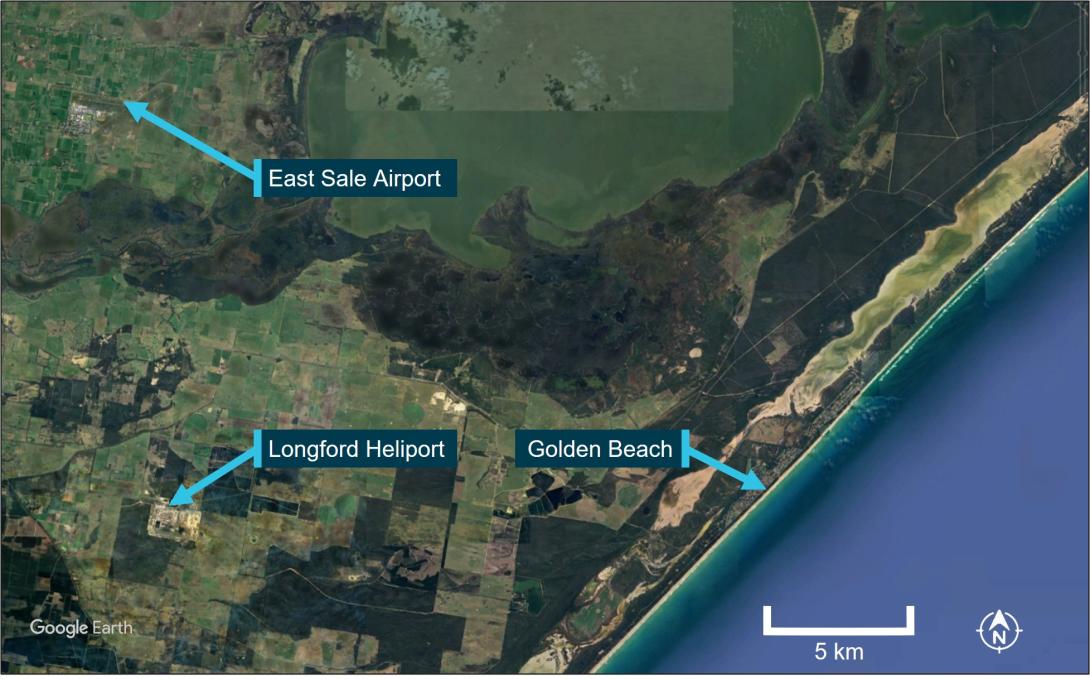
Source: Google Earth, annotated by the ATSB
Inflight weather observations
After a routine departure, the crew recalled observing a bank of fog along the coastline as the helicopter approached the training area. The instructor estimated that the fog bank was less than one kilometre from shore at the time. As the exercise began the flight crew reported that the fog began to obscure the shoreline near Golden Beach. However, clear skies were visible to the north and north‑east, while a large easterly swell created rough sea conditions below.
During the exercise, the flight crew reported that the helicopter was manoeuvred closer to the fog, which was situated on the left side of the helicopter, where the instructor was seated.
Operator procedures
Hoisting
Hoisting operations require coordination between all crew members and adherence to procedures and safety protocols. The hoist system, equipped with a cable and hook, facilitates the controlled retrieval of individuals or equipment, sometimes in challenging environments, such as water or rugged terrain.
Esso Australia hoisting crew compliment
Esso Australia hoist operations required a minimum crew of two flight crew, a hoist operator, and a wireman, each with defined roles (Table 1).
Table 1: Crew member location and roles
Crew member | Location | Role |
Captain | Right side pilot seat | Oversees all aspects of the flight, especially during rescue operations, and briefs all crew members prior to departure. |
Copilot | Left side pilot seat | Manages flight planning, navigates, monitors radios and helicopter systems, and assists with hoist operations as necessary. |
Hoist operator (HO) | Cabin | Prepares rescue equipment, conducts pre-hoist checks, ensures cabin security, operates the hoist, and guides the pilot during hoisting. |
Wireman | Cabin | Assists the HO, manages personal safety, and is prepared to descend on the hoist cable if needed. |
The flight crew reported that the instructor and check aircrewman acted as copilot and wireman during the occurrence.
Hoist patterns and limitations
When conducting hoist exercises, helicopters typically follow a structured racetrack pattern approach, initially at 60 kt about 200–500 ft above obstacles. After approaching the site, the crew hover at a height below 100 ft over the target area to facilitate a stable hoisting environment.
The AW139 rotorcraft flight manual outlined the following operational limitations for hoist operations:
- maximum 80 kt maximum forward flight speed during hoist operations
- maximum 80 kt for opening/closing cabin door or 100 kt when door is locked open
- fly manually or attentively when RHT mode is engaged.
The flight data from the occurrence revealed that the helicopter exceeded airspeed limitations for hoisting and the main door in the locked open position (See section titled Recorded information).
Post hoist procedures
Following a hoisting task, the hoist operator (HO) would secure the cabin and equipment, complete a post‑hoist checklist with the pilot monitoring (PM) using the challenge and response methodology,[15] and confirm the completion of the checklist items. The PM then completes the post‑hoist checks with the HO using the same checklist methodology (Table 2).
Table 2: Post hoist procedure and checks
Procedure | Actions |
Post-hoist procedure
|
|
Post-hoist check
|
|
After take-off check |
|
The crew recalled that before they departed the exercise site, the post‑hoist procedures and checks had not been performed.
Automation use
The use of automation for day VFR offshore flights, was detailed in the operator’s exposition stated as follows:
The advanced avionics suite in the AW139 promotes a high level of safety and crew situational awareness when used correctly. When not used correctly or understood, the opposite can occur allowing dangerous deviations and loss of situational awareness to quickly manifest.
ESSO Australia policy is for the flight management systems, multi-function control display units and avionics to be operated at a level that provides optimum navigation, communication and traffic awareness to the crews without drawing too much attention ‘inside the cockpit’. At all times, it is the responsibility of the PF to maintain effective control of the helicopter and its flight path/situation.
Handover and takeover procedures
Handover procedures in the operator exposition detailed the protocols flight crews must follow when transferring control to another pilot. The relinquishing pilot is required to state, ‘handing over,’ and the receiving pilot confirm by stating ‘taking over’ while placing their hands and feet on the controls. The first pilot then removes their inputs, ensuring clear role delineation. Handover drills must incorporate an active flight director, with no alternative transfer methods allowed.
The flight crew recalled that there was no verbalisation of the transfer of control during the recovery following the EGPWS alert.
The handover procedure was intended to ensure clear communication and role clarity by requiring the relinquishing pilot to state, 'handing over,' with the flying pilot to respond 'taking over' while actively taking control. These structured procedures are critical for maintaining operational safety and minimising risks during complex or dynamic situations. Neither pilot recalled referencing any rehearsed procedures in response to the inadvertent entry to IMC during the recovery. Additionally, they did not recall specific training in the helicopter or the simulator for EGPWS recovery.
Enhanced ground proximity warning procedures
As part of the pre‑flight checks, flight crews were required to test the EGPWS to confirm the serviceability of the system. The operator exposition also required that flight crews must respond to EGPWS cautions and warnings in marginal weather.
Neither pilot recalled any prescribed operator procedures that were referenced during the recovery following the EGPWS warnings during the occurrence.
Offshore operations
Standard procedures required crew to activate offshore mode once established beyond the coastline and to deactivate once established onshore. This selection of the offshore mode is verified by the PM and PF using the ‘coast check’ contained in the AW139 normal checklist.
Both flight crew recalled that offshore mode was activated on the EGPWS for the duration of the hoisting exercise.
Operator training
The operator’s exposition described the training and checking policies and procedures, and the regulatory requirements of the applicable Civil Aviation Safety Regulations (CASR). The operator maintained a training and checking organisation authorised by an instrument issued by the Civil Aviation Safety Authority (CASA). This training was conducted by nominated personnel put forward by the operator.
Upon completion of induction training, crews were required to complete recurrent training which included an operational proficiency check (OPC) for each type of operation.
Crew hoisting training
Crew hoisting training was provided by the operator as part of the combined search and rescue (SAR)/hoisting OPC. Additionally, a standalone hoisting OPC was conducted at 6‑monthly intervals. While the check events alternated every 6 months, they remained valid for 12 months from the date of completion.
The hoisting OPC assessed theoretical and practical aspects of hoisting, encompassing all phases of flight, with technical and non‑technical skills being assessed by approved personnel.
The instructor and captain conducted their hoisting OPC on 4 December 2023 and 23 October 2023 respectively. The instructor also conducted the captain’s combined SAR/hoist OPC on 16 May 2024, which included the same hoisting elements of the training that took place during the occurrence.
Scenarios involving a recovery from the hover with a prescribed low‑level inadvertent instrument meteorological conditions (IIMC) operating procedure were not included in the biannual SAR/hoist syllabus at the time of the occurrence.
Recurrent simulator training
Esso Australia conducted emergency OPC check every 6 months, in accordance with CASR 61 requirements in an AW139 full flight simulator. The emergency OPC satisfies the requirements for the type rating and low-level flight reviews.
All sequences flown were in a reduced visual cueing environment to mimic weather conditions that are regularly encountered when conducting flight operations in the Bass Strait.
Flight crews would encounter a simulated technical failure in reducing visibility at ‘low‑level’ below 500 ft leading to IIMC. This scenario would lead to either a ditching, or recovery in IIMC. In the case of the latter, this scenario required the flight crew to recover to a safe altitude, which the instructor and captain completed as a crew pairing on 18 September 2023.
Flight crew also received briefings on the 4 ‘Cs’ (Control, Climb, Course and Communicate ) IIMC recovery technique (International Helicopter Safety Team).
Scenarios involving a recovery from the hover in IIMC conditions with a prescribed operating low‑level IIMC procedure were not included in the biannual simulator training syllabus at the time of the occurrence.
Esso Australia crew resource management training
Esso Australia conducted annual crew resource management (CRM) training every 12 months, in accordance with CASR 119 and CASR 133 requirements. The training modules covered:
- human performance and limitations
- situational awareness
- decision-making
- teamwork and communication
- threat and error management
- workload management and automation.
EGPWS training
The operator training requirements required that crew completed training specific to the Honeywell MK XXII‑30 EGPWS system installed on its AW139 fleet. The EGPWS training was incorporated into the AW139 differences training, which all flight crew had to complete during their initial entry into the Esso Australia check and training system. This included both theoretical knowledge and practical exercises to ensure proficiency in managing system operations. The training covered:
- general overview of the system
- normal procedures including setup for flight operations, functionality, general actions during an alert, and a demonstration of the self-test
- limitations of the system
- emergency and malfunction procedures.
The operator stated that EGPWS training events in the simulator had ceased in 2021 due to inaccuracies of the simulator‑generated warnings and alerts. As a result, Esso Australia flight crew underwent technical refresher ground training, which included a module dedicated to EGPWS. The instructor and captain conducted their EGPWS refresher training on 19 September 2023.
Recorded information
The AW139 helicopter is equipped with a multipurpose flight data recorder (MPFDR). The MPFDR combines both a flight data recorder (FDR) and a cockpit voice recorder (CVR), capturing helicopter data and audio.
Personnel from Esso Australia secured a copy of the FDR data for analysis and provided a copy of that data to the ATSB. The files were downloaded and confirmed to have contained flight data recorded during the EGPWS occurrence on 19 August 2024 from the MPFDR fitted to AW139 VH‑EXK. Although FDR data was available, no CVR data was retrieved for this occurrence due to the helicopter operating multiple flights in the days following the occurrence.
The recorded flight data captured parameters such as altitude, airspeed, control inputs and the activation of systems such as the RHT, FTR and EGPWS alerts. This data enabled a detailed reconstruction of the flight, providing insights into the helicopter’s performance and crew actions leading up to the event.
Recorded data
Just prior to the EGPWS event, an airspeed exceedance was identified, with the NR at 102% when the airspeed was above 90 kt. This persisted for a period of 3 seconds and occurred 2 seconds prior to the activation of the EGPWS system.
The EGPWS event trigger was identified as a combination of the radar altitude reducing below 150 ft as the airspeed exceeded 100 kt. The minimum radar altitude reached was 140 ft.
The MPFDR data revealed multiple key events during the event (Table 3).
Key events
Local time | Event | Radio Height feet AGL |
Pitch +/- ° |
Groundspeed knots |
Computed airspeed knots |
Vertical speed +/- fpm |
0908:08 | Collective beep AFT active; collective FTR active | 72 | 5.976 | 0 | 0 | -32 |
0908:18 | Groundspeed begins increasing collective beep AFT active collective FTR active | 85 | 5.625 | 2 | 0 | 128 |
0908:38 |
Computed airspeed above 0, helicopter climbing Collective FTR active; over the next ten second period, the collective FTR is active for 8 seconds |
154 | 0.176 | 28 | 38.5 | 192 |
0908:50 | Rad alt peak 185, airspeed increasing through 75 kt collective FTR active | 185 | -5.976 | 66 | 75.5 | -64 |
0908:51 |
Collective trim engaged negative vertical speed begins developing |
183 | -6.855 | 70 | 79.5 | -128 |
0908:55 | Collective trim disengaged NR exceedance - >90 kt at 102% for 3 second duration | 173 | -2.109 | 82 | 93.75 | -224 |
0908:59 | Collective trim engaged; negative vertical speed is reducing | 153 | -1.406 | 90 | 99.5 | -224 |
0909:00 | Collective FTR active; EGPWS alert is activated for one second, followed by the EGPWS warning for 5 seconds | 147 | -0.879 | 90 | 101.5 | -64 |
0909:03 | Collective FTR active; minimum altitude reached | 140 | 10.019 | 88 | 99.5 | 832 |
0909:07 | Collective FTR active; following this, the collective FTR is active for 41 seconds of the following 54 seconds, as the helicopter climbs through 680 ft. | 215 | 13.007 | 76 | 89.75 | 2048 |
Source: Operator supplied flight data recorder, tabulated by the ATSB
The recorded pitch changes during 60 seconds of flight data, showing a pitch range of up to 19°, coupled with fluctuating airspeed above limitations and unstable vertical speed, demonstrate an unstable aircraft profile during departure.
Operator internal investigation
Following the occurrence, Esso Australia conducted an internal investigation, concluding that inadequate procedures and work standards were the primary factors contributing to the incident. The internal investigation identified the root cause as:
Deficiencies in procedures regarding Search and Rescue (SAR) Training in the vicinity of fog.
Related occurrences
The following 2 ATSB investigations highlight the risks of inadvertent IMC encounters at close proximity to the ground and demonstrate the importance of rehearsed recovery drills in these situations. In both instances, the flight crew were IFR rated, and the helicopters were also IFR equipped.
These occurrences emphasise the effects of spatial disorientation[16] due to powerful and misleading orientation sensations during times of reduced visual cues, which can affect any pilot, no matter what their level of experience.
ATSB investigation AO-2016-160
On 21 October 2016, the crew of a BK 117‑C2 were returning to their home base from Crookwell, New South Wales, after carrying out an emergency medical service mission. The flight was conducted under night visual flight rules with the aid of a night vision imaging system.
Conditions were marginal and, on departure, the helicopter entered low cloud. The aircrew officer declared loss of visibility on take‑off. The pilot had poor visibility ahead yet could see well to the right. The pilot thought visibility would improve as they passed ground lighting that was reflecting in raindrops on the canopy.
The visibility did not improve, and the pilot slowed the aircraft to maintain visual meteorological conditions. The low‑speed manoeuvre resulted in an undesired aircraft state and an EGPWS warning activated. The pilot conducted an inadvertent IMC drill, restabilised control, and continued the flight before landing safely.
ATSB investigation AO-2018-039
On 13 May 2018, the crew of a Leonardo Helicopters AW139 departed Darwin, Northern Territory, to search for an active emergency position‑indicating radio beacon. The crew flew under night visual flight rules with support of a night vision imaging system.
During an approach to a potential target, smoke from nearby bushfires affected visibility and the helicopter developed an uncommanded high rate of descent. The aircrew officer, in the rear of the helicopter, called ‘Climb! Climb! Climb!’, and the pilot regained control with a rehearsed recovery drill.
During the recovery procedure, the power demand exceeded airframe limitations. This exceedance went undetected, and the helicopter was flown on a second sortie that same evening.
Safety analysis
Introduction and background
After concluding hoist training exercises near Golden Beach, Victoria, a Leonardo Helicopters AW139, registered VH‑EXK and operated by Esso Australia, inadvertently entered instrument meteorological conditions (IMC), which resulted in an enhanced ground proximity warning system (EGPWS) alert.
This analysis will examine factors contributing to the occurrence, including:
- crew decision‑making
- the transition from visual meteorological conditions (VMC) to IMC
- the effects of spatial disorientation
- control inputs during the event
- operator procedures
- crew response to the EGPWS alert.
Departure
During the hoisting exercise, both flight crews observed clear skies on the captain’s side of the helicopter to the north and north‑east of their position. Meanwhile fog approached from the north‑west on the instructor’s side and the instructor elected to depart and announced their intention to climb. Climbing immediately in the vicinity of fog may not have been necessary, as manoeuvring to the north or north‑east would have increased the distance from the fog. However, as the helicopter climbed, it encountered fog and the instructor immediately elected to depart, attempting to climb above the fog while tracking north‑west toward the shoreline.
As the instructor departed the training area for Longford at the conclusion of the exercise, the helicopter remained in a hoisting configuration. This meant the hoist was extended approximately 40 ft below the helicopter, the main cabin door was locked open and the helicopter’s main rotor RPM was set to 102%.
After hoisting exercises, the post‑hoist procedure required the hoist operator (HO) to stow the hoist, secure the cabin and advise the pilot monitoring (PM) prior to climbing. The PM would assist the HO in completing the post‑hoist check, confirming the crew actioned the appropriate items. However, due to the encroaching fog, the instructor elected to climb, lost visual references and reactively began to accelerate and climb the helicopter before completing the post‑hoist check.
These procedures ensure the helicopter is properly configured for departure, including securing the cabin, stowing the hoist and adjusting the main rotor RPM to 100%, once the helicopter accelerates through 80 kt.
As the helicopter accelerated the check aircrewman voiced their concern about departing, likely due to the present configuration not being suitable for forward flight.
Completing the post‑hoist procedure before departing would have removed the risk associated with potential interference from the extended hoist cable and exceeding the flight envelope limitations with the helicopter in the hoisting configuration. Additionally, by completing these procedures in a stationary position, the captain could have more effectively monitored the flight path during departure.
At the time of departure, the captain, who was the PM, was focused on marking the GPS position of the training aid in the flight management system (FMS) to facilitate retrieval during the next exercise. While this task had operational value, it distracted the captain from monitoring the helicopter’s dynamic state and assisting the instructor with flight path management, navigation and maintaining situational awareness. However, the captain was unaware of the instructor’s intention to depart, likely due to the expectation that the completion of the post‑hoist procedure had not been completed as a prerequisite to climb away.
Contributing factor The instructor hastily departed the training area, due to encountering fog, before the hoist was secured with the door open, and while the captain as pilot monitoring was still occupied recording the training aid position. |
Spatial disorientation
The instructor departed the training area on a north‑westerly heading, toward the shoreline and the previously observed fog. The instructor achieved a relatively stable climb, albeit with a steadily increasing forward airspeed. The helicopter's altitude peaked at 185 ft at 72 kt; however, as the climb progressed, the helicopter inadvertently entered IMC, depriving the crew of external visual references.
Both flight crew recall being in VMC when the climb commenced with the instructor verbalising their intention to climb above the fog toward an area of VMC. According to the instructor the helicopter entered fog as the helicopter began to climb while the captain was looking down and didn’t observe the transition to IMC.
The flight data recorder (FDR) captured altitude and airspeed fluctuations, consistent with flight control inputs from the pilot flying being uncertain of the flight path, including a nose‑down attitude and airspeed increasing through 80 kt. Therefore, without visual cues, the instructor likely became subject to the effects of spatial disorientation. This condition significantly impairs a pilot's ability to accurately interpret attitude, altitude and airspeed.
Contributing factor After inadvertently entering instrument meteorological conditions, the instructor (pilot flying) became spatially disorientated. |
Operating in degrading visibility creates ambiguity, stalling decision‑making as flight crew face conflicting situational cues (Orasanu, Martin, & Davidson, 2001). Continued reliance on visual cues in these scenarios can draw attention away from critical instrument readings (Summerfield & Enger, 2009). Coupled with the inherent instability of medium‑sized helicopters, these cognitive tendencies further increase the risks associated with spatial disorientation in degraded visibility environments.
Unstable flight
Frequent engagement and disengagement of the collective force trim release (FTR) when the radar height hold (RHT) was active further destabilised the helicopter, causing altitude and airspeed fluctuations. The operator exposition highlighted the potential risks by stating that the incorrect use of the AW139's automation systems can lead to dangerous deviations and loss of situational awareness. Additionally, the AW139's rotorcraft flight manual (RFM) stated that the helicopter must be attentively flown during hoisting operations using the RHT function. The FTR switch demands disciplined use, as its unintentional instinctual engagement can lead to unintended control inputs. As a result, crews must carefully monitor their inputs and selections when using the RHT and FTR functions. Pilots tend to overestimate their ability to continue to control the aircraft when visual references are lost (Wiggins, Hunter, O'Hare, & Martinussen, 2012). During the periods of high crew workload, the interactions of these systems added to the difficulties in sustaining stability in the degraded visual environment.
The combination of spatial disorientation, intermittent collective FTR use, flight control inputs and an overall impaired situational awareness of the crew, culminated in the helicopter being still in the hoisting configuration, whilst descending below 150 ft above sea level and exceeding 100 kt.
This resulted in flight envelope exceedances of:
- operation with the hoist cable extended
- the right cabin door in the open position
- operation with the main rotor RPM at 102%.
This posed additional risks, including potential aircraft damage as a result of the hoist cable interfering with the tail rotor, damage to the aircraft due to slipstream pressure on the door. The situation reached a critical point when the EGPWS issued a terrain alert, signalling the imminent risk of collision with terrain.
Contributing factor The instructor's attempt to leave IMC, while being spatially disorientated, resulted in control inputs that led to the helicopter entering an unstable state while still in IMC, triggering a terrain alert below 150 ft, and airspeed exceedances for operations with the main rotor RPM at 102%, the door open and hoist extended. |
Recovery
Immediately following the EGPWS alert, the captain took control of the helicopter without a formal handover from the instructor by reactively pulling back on the cyclic. Prior to assuming control, the captain was occupied with entering GPS coordinates into the flight management system (FMS), which diverted their attention from monitoring the helicopter's flight path. This meant they were not able to actively observe changes to the dynamic state of the helicopter and missed the early indications of loss of spatial orientation by the PF due to the degrading visibility.
Due to a lack of visual cues, the captain was unsure of their altitude and reactively pulled back on the cyclic to arrest the helicopter's forward momentum and gain altitude. After the helicopter was established in a climb and following a brief exchange, control of the helicopter was transferred back to the instructor.
The captain bypassed handover protocols, likely due to the receipt of the EGPWS warning and perceived rapidly escalating events. Operator procedures also mandate that flight crews respond promptly to EGPWS warnings.
Reactive assumption of control by the non‑flying pilot had the potential to introduce further distractions, conflicting control inputs or further inappropriate control inputs in an already dynamic and demanding environment. Although the captain bypassed standard handover procedures, the absence of a structured handover also highlights the difficulties of managing dynamic situations under pressure and balancing conflicting demands.
Other factor that increased risk Prior to gaining situational awareness and without an appropriate control handover, the captain reactively assumed control of the helicopter after the terrain warning, increasing the risk of control conflict between the 2 crew. |
Operator procedures
Esso Australia did not provide crew with structured procedures for managing inadvertent entry into IMC and EGPWS alerts during hoist operations. Although the Esso Australia exposition required a pilot response to EGPWS alerts, this did not include specific guidance for managing such alerts. While training covered general EGPWS functionality, it did not include scenario‑based drills for complex situations involving degraded visibility or low-level operations.
Consequently, responses to alerts were reactive, with the crew relying on instinct rather than following a predefined recovery procedure. The absence of predefined inadvertent IMC‑specific recovery actions also exposed the crew to the cognitive effects and demands of operating in degraded visual environments.
The related occurrences further demonstrate the effectiveness of structured recovery protocols and crew resource management (CRM) in stabilising helicopters during degraded visual conditions. The absence of similar predefined procedures that the crew could have utilised, underscores the need for enhanced training and clear protocols to manage scenarios involving inadvertent IMC and EGPWS alerts.
Other factor that increased risk Esso Australia did not have a procedure for a helicopter recovery from inadvertent IMC during hoist operations or recovery procedures for EGPWS alerts or advisories. (Safety issue) |
Captain’s decision‑making
In a matter of seconds following the initial EGPWS caution, the captain arrested the rate of descent and transitioned into a climb while reducing the forward airspeed of the helicopter. The captain’s intervention immediately reduced the risk of a collision with terrain.
Before assuming control, the captain was able to identify and vocalise the increasing airspeed in an attempt to illicit corrective action from the instructor. A progressive intervention strategy is initiated by communicating a flightpath deviation (alert), then suggesting a course of action (advocacy and assertion) and then directly intervening, if necessary (Civil Aviation Safety Authority 2020). Despite bypassing Esso Australia handover protocols, the captain effectively recognised and responded to the EGPWS alerts and the reduced proximity to terrain.
Although the captain’s initial degraded situational awareness and lack of visual cues limited their initial understanding of the situation, their decision to establish control of the aircraft during a critical situation was sound.
Their decision to prioritise scanning the instruments to regain situational awareness during the event contributed to a successful recovery. The decisive nature of their intervention further underscores the importance of training and rehearsed recovery actions to mitigate the risks of spatial disorientation in degraded visual environments.
Other finding The captain's control inputs stopped the vertical descent and established the helicopter in a climb, which reduced the risk of collision with terrain. |
Findings
ATSB investigation report findings focus on safety factors (that is, events and conditions that increase risk). Safety factors include ‘contributing factors’ and ‘other factors that increased risk’ (that is, factors that did not meet the definition of a contributing factor for this occurrence but were still considered important to include in the report for the purpose of increasing awareness and enhancing safety). In addition ‘other findings’ may be included to provide important information about topics other than safety factors. Safety issues are highlighted in bold to emphasise their importance. A safety issue is a safety factor that (a) can reasonably be regarded as having the potential to adversely affect the safety of future operations, and (b) is a characteristic of an organisation or a system, rather than a characteristic of a specific individual, or characteristic of an operating environment at a specific point in time. These findings should not be read as apportioning blame or liability to any particular organisation or individual. |
From the evidence available, the following findings are made with respect to the loss of control in flight involving Leonardo Helicopters AW139, VH‑EXK, 19 km east of Longford Heliport, Victoria, on 2 August 2024.
Contributing factors
- The instructor hastily departed the training area, due to encountering fog, before the hoist was secured with the door open, and while the captain as pilot monitoring was still occupied recording the training aid position.
- After inadvertently entering instrument meteorological conditions, the instructor (pilot flying) became spatially disorientated.
- The instructor's attempt to leave IMC, while being spatially disorientated, resulted in control inputs that led to the helicopter entering an unstable state while still in IMC, triggering a terrain alert below 150 ft, and maximum airspeed exceedances for operations with the main rotor RPM at 102%, the door open and hoist extended.
Other factors that increased risk
- Prior to gaining situational awareness, and without an appropriate control handover, the captain reactively assumed control of the helicopter after the terrain warning, increasing the risk of control conflict between the 2 crew.
- Esso Australia did not have a procedure for a helicopter recovery from inadvertent IMC during hoist operations or recovery procedures for EGPWS alerts or advisories. (Safety issue)
Other findings
- The captain's control inputs stopped the vertical descent and established the helicopter in a climb, which reduced the risk of collision with terrain.
Safety issues and actions
Central to the ATSB’s investigation of transport safety matters is the early identification of safety issues. The ATSB expects relevant organisations will address all safety issues an investigation identifies. Depending on the level of risk of a safety issue, the extent of corrective action taken by the relevant organisation(s), or the desirability of directing a broad safety message to the Aviation industry, the ATSB may issue a formal safety recommendation or safety advisory notice as part of the final report. All of the directly involved parties are invited to provide submissions to this draft report. As part of that process, each organisation is asked to communicate what safety actions, if any, they have carried out or are planning to carry out in relation to each safety issue relevant to their organisation. Descriptions of each safety issue, and any associated safety recommendations, are detailed below. Click the link to read the full safety issue description, including the issue status and any safety action/s taken. Safety issues and actions are updated on this website when safety issue owners provide further information concerning the implementation of safety action. |
Crew training
Safety issue number: AO-2024-045-SI-01
Safety issue description: Esso Australia did not have a procedure for a helicopter recovery from inadvertent IMC during hoist operations or recovery procedures for EGPWS alerts or advisories.
Safety action not associated with an identified safety issue
Whether or not the ATSB identifies safety issues in the course of an investigation, relevant organisations may proactively initiate safety action in order to reduce their safety risk. The ATSB has been advised of the following proactive safety action in response to this occurrence. |
Additional safety action by Esso Australia
In addition to developing training and procedures for inadvertent IMC recovery from a search and rescue and hoisting scenario, the operator identified several actions to be taken which included:
- discussing the weather phenomena and the possibility for sudden loss of visibility with crews
- updating pre-flight training brief to highlight the need to maintain a safe distance to fog or cloud
- developing training focusing on the radar height hold function of the AW139
- including upset recovery training in CRM.
Glossary
CASA | Civil Aviation Safety Authority |
CASR | Civil Aviation Safety Regulations |
CRM | Crew resource management |
CVR | Cockpit voice recorder |
EGPWS | Enhanced ground proximity system |
FDR | Flight data recorder |
FTR | Force trim release |
FMS | Flight management system |
HO | Hoist operator |
IIMC | Inadvertent IMC |
IMC | Instrument meteorological conditions |
JSA | Job safety analysis |
MPFDR | Multi-purpose flight data recorder |
NR | Rotor speed |
OPC | Operational proficiency check |
PF | Pilot flying |
PFD | Primary flight display |
PM | Pilot monitoring |
RFM | Rotor flight manual |
RHT | Radar height hold |
SAR | Search and rescue |
SPECI | A special report of meteorological conditions, issued when one or more elements meet specified criteria significant to aviation |
VMC | Visual meteorological conditions |
VFR | Visual flight rules |
Sources and submissions
Sources of information
The sources of information during the investigation included:
- Airservices Australia
- Bureau of Meteorology
- captain and instructor of VH-EXK
- Civil Aviation Safety Authority
- flight data from VH-EXK.
References
Australian Transport Safety Bureau. (2007). An overview of spatial disorientation as a factor in aviation accidents and incidents. ATSB Aviation Research and Analysis Report B2007/0063. Retrieved fromhttps://www.atsb.gov.au/publications/2007/b20070063
Civil Aviation Safety Authority. (2020). Advisory Circular, Upset prevention and recovery training, December 2020 (121-03v1.0). Retrieved from https://www.casa.gov.au/upset-prevention-and-recovery-training
Hoh, R. (1990). The effects of degraded visual cueing and divided attention on obstruction avoidance in rotorcraft, Report prepared for the United States Federal Aviation Administration (DOT/FAA/RD-90/40). Retrieved fromhttps://apps.dtic.mil/sti/citations/ADA380260
International Helicopter Safety Team. (n.d.). Training Fact Sheet – Inadvertent Entry Into Instrument Meteorological Conditions (IIMC). Retrieved from https://ushst.org/IIMC/Bulletin%20IIMC.doc
L, O. J. (1998). Errors in aviation decision making: A factor in accidents and incidents. In Proceedings of the Workshop on Human Error, Safety, and Systems Development. 100-107.
Orasanu J., Martin, L., & Davidson, J., (2001). Cognitive and contextual factors in aviation accidents, Linking expertise and naturalistic decision making, 209–226.
Summerfield C & Enger T. (2009). Expectation (and attention) in visual cognition, Trends in Trends in Cognitive Sciences. 13(9). 403-409.
United Kingdom Civil Aviation Authority. (2007). Helicopter flight in degraded visual conditions (Paper 2007/03). Retrieved fromwww.caa.co.uk.
Wickens CD & McCarley JS. ( 2008). Applied Attention Theory, CRC Press, Boca Raton.
Wiggins, M. W., Hunter, D. R., O’Hare, D., & Martinussen, M. (2012). Characteristics of pilots who report deliberate versus inadvertent visual flight into instrument meteorological conditions’, Safety Science. 50(3). 472-477.
Submissions
Under section 26 of the Transport Safety Investigation Act 2003, the ATSB may provide a draft report, on a confidential basis, to any person whom the ATSB considers appropriate. That section allows a person receiving a draft report to make submissions to the ATSB about the draft report.
A draft of this report was provided to the following directly involved parties:
- captain and instructor of VH-EXK
- Esso Australia
- Bureau of Meteorology
- Civil Aviation Safety Authority
Submissions were received from:
- Esso Australia
- Bureau of Meteorology
- Civil Aviation Safety Authority
The submissions were reviewed and, where considered appropriate, the text of the report was amended accordingly.
Purpose of safety investigationsThe objective of a safety investigation is to enhance transport safety. This is done through:
It is not a function of the ATSB to apportion blame or provide a means for determining liability. At the same time, an investigation report must include factual material of sufficient weight to support the analysis and findings. At all times the ATSB endeavours to balance the use of material that could imply adverse comment with the need to properly explain what happened, and why, in a fair and unbiased manner. The ATSB does not investigate for the purpose of taking administrative, regulatory or criminal action. TerminologyAn explanation of terminology used in ATSB investigation reports is available here. This includes terms such as occurrence, contributing factor, other factor that increased risk, and safety issue. Publishing informationReleased in accordance with section 25 of the Transport Safety Investigation Act 2003 Published by: Australian Transport Safety Bureau © Commonwealth of Australia 2025
Ownership of intellectual property rights in this publication Unless otherwise noted, copyright (and any other intellectual property rights, if any) in this report publication is owned by the Commonwealth of Australia. Creative Commons licence With the exception of the Commonwealth Coat of Arms, ATSB logo, and photos and graphics in which a third party holds copyright, this report is licensed under a Creative Commons Attribution 4.0 International licence. The CC BY 4.0 licence enables you to distribute, remix, adapt, and build upon our material in any medium or format, so long as attribution is given to the Australian Transport Safety Bureau. Copyright in material obtained from other agencies, private individuals or organisations, belongs to those agencies, individuals or organisations. Where you wish to use their material, you will need to contact them directly. |
[1] Pilot flying (PF): focuses on handling the helicopter during hoisting operations.
[2] Pilot monitoring (PM): manages non-hoist communications, logs positions, monitors performance, and completes in‑flight checks, especially for height and potential obstructions.
[3] Visual flight rules (VFR): a set of regulations that permit a pilot to operate an aircraft only in weather conditions generally clear enough to allow the pilot to see where the aircraft is going.
[4] Collective: a primary helicopter flight control that simultaneously affects the pitch of all blades of a lifting rotor. Collective input is the main control for vertical velocity.
[5] See Helicopter information, Autopilot and radar height hold
[6] Instrument meteorological conditions (IMC): weather conditions that require crews to fly primarily by reference to instruments, and therefore under instrument flight rules (IFR), rather than by outside visual reference.
[7] See Helicopter information, Powerplant.
[8] Cyclic: helicopter control mechanism for periodically varying the blade angle of each rotor blade, producing a tilt in the tip-path plane and effecting motion in a desired direction
[9] Instrument flight rules (IFR): rules which allow properly equipped aircraft to be flown under instrument meteorological conditions (IMC)
[10] Helideck: A heliport located on a fixed or floating offshore facility such as an exploration and/or production unit used for the exploitation of oil or gas.
[11] External load: carrying or towing a load outside an aircraft in flight and includes training for such an operation.
[12] Category A: In relation to rotorcraft, means a multi-engine rotorcraft that is capable of operation using take-off and landing data scheduled under a critical engine failure concept, which assures adequate designated ground or water area and adequate performance capability for continued safe flight, or safe rejected take-off in the event of engine failure, as mentioned in the rotorcraft’s flight manual.
[13] A dual action spring permits force‑feel hands on flying while the force trim is engaged. A pilot moving the flight controls without releasing the force trim results in full hands‑on controllability with control force feedback to the pilot. As the pilot releases the control to resume hands‑off flying, the spring returns the collective to its neutral position against the force trim.
[14] JSA: job safety analysis – crew briefing review of operational data, tech log details and rotor flight manual aircraft performance.
[15] Challenge and response procedures apply to multi‑crew operations, where checklist items are called by one crew member and either checked or completed by another.
[16] Spatial disorientation occurs when a pilot does not correctly sense the position, motion and attitude of an aircraft relative to the surface of the Earth. More information about spatial disorientation can be found in the ATSB aviation research and analysis report B2007/0063, An overview of spatial disorientation as a factor in aviation accidents and incidents.