At 1702 central standard time on 14 June 2004, a Bell Helicopter Company 206B(II) Jetranger, registered VH-PHF, was being operated for a medical evacuation from Deep Well, NT, to Alice Springs. About 5 NM south-west of Alice Springs Airport, while cruising at 500 ft above ground level at 100 kts, the pilot felt a vibration and heard a loud bang accompanied by a reduction in main rotor torque. The pilot immediately placed the helicopter into an autorotative descent and broadcast a MAYDAY1 to the Alice Springs Air Traffic Control aerodrome controller. The pilot landed the helicopter in a clearing and the five occupants were uninjured.
Initial inspection of the helicopter by the operator revealed that the KAflex2 driveshaft between the engine free-wheeling unit and the main transmission had failed. The failed shaft and its components were removed from the helicopter and forwarded to the Australian Transport Safety Bureau (ATSB) for metallurgical examination. The examination found that the failures had occurred in the arms of the web elements, with all of the fractures typical of gross-overload failure from either a single or small number of cycles. Of significant interest was the separation of one of the flex frame unions (see Figure 1). This section showed evidence of wear and deformation consistent with looseness of the bolted joint fastener. Fatigue cracking had initiated from the bore or worn surfaces of the frame and propagated radially away from the hole, intersecting the side of the frame and freeing the connection.
Figure 1: Worn fastener bore and fracture in flex frame. Arrows indicate the point
of fatigue crack initiation and the direction of propagation.
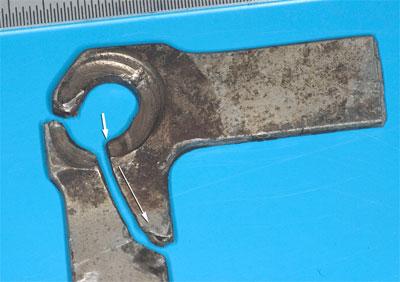
Maintenance history
The helicopter's Maintenance Release was valid until 27 November 2004 or 12,351.80 hours in service, whichever occurred first. At the time of the failure, the helicopter had 12,168.25 hours in service. The operator had responsibility for the maintenance of the helicopter, which was conducted under a valid Certificate of Approval. The helicopter was operated in the Normal category, Day VFR.
The helicopter was maintained as a Class B type aircraft, with the airframe maintenance conducted in accordance with the manufacturer's prescribed maintenance procedures. In this instance, the Bell Helicopter Textron Company 206 Maintenance Manual BHT-206A/B-SERIES-MM-1 was identified in the Logbook Statement as the primary documentation. However, the driveshaft manufacturer's documentation was not identified as required supplemental documentation in that statement. The inspection schedule worksheets for maintenance were copied, for use by the maintenance personnel, directly from the airframe manufacturer's manuals. No supplemental maintenance inspection sheets were incorporated into any of the maintenance worksheet packages that specifically identified maintenance actions to be performed for the KAflex driveshaft.
The helicopter underwent a 300-hourly inspection for the issue of a maintenance release at Moorabbin, Victoria on 27 November 2003. No entries were recorded on the maintenance release with regard to any daily or periodic inspection requirements specific to the KAflex driveshaft.
Main driveshaft
The Jetranger was delivered with a proprietary designed main driveshaft. The driveshaft, which comprised a spherical coupling at either end of a torque shaft, was designed to transmit power from the engine freewheeling unit output adapter to the main transmission input quill. The engine's output shaft speed was around 6,000 RPM3 during helicopter operation. The application of power and flight and ground loads all contributed to drive line misalignment during operation. The spherical coupling design compensated for that misalignment under normal operating conditions. The main driveshaft was subject to ongoing monitoring through heat sensitive temperature indicators that detected overheating caused by inadequate lubrication, wear, or excessive misalignment of the drive train elements. Periodic maintenance of the driveshaft included disassembly, inspection and lubrication in accordance with the Bell Helicopter Textron Company 206 Maintenance Manual, to ensure the continuing airworthiness of the driveshaft.
On 19 January 1998, at 8,055.9 hours aircraft total time in service, the Bell manufactured engine-to-transmission driveshaft in the helicopter had been replaced with a KAflex unit. The new driveshaft was designed to replace the proprietary unit and had been marketed as providing reduced maintenance, longer time between overhauls, and greater reliability.
The Kamatics Corporation web page advised:
Helicopter flight manoeuvres generate high misalignment between the engine and the transmission, which must be accommodated by the connecting driveshaft. Such driveshafts, which rotate at speeds over 6000 RPM, often incorporate grease lubrication and seals. Designs of this type are susceptible to loss of lubrication, which results in overheating and possible failure, a major safety concern.
The KAflex driveshaft is a mechanical drive coupling which requires no lubrication or seals, and transmits power while accommodating high angular misalignment and length change through the use of flexible rectangular frames. These frames are bolted together at the corners in a truss-like arrangement, which are attached to shaft end fittings to allow for drop-in installation in the drive line. A fail-safe feature enables the coupling to continue to transmit power even in the unlikely event of a failure in a load carrying member.
KAflex driveshafts are custom designed for specific applications and selected because they offer superior, maintenance-free performance with extended 'on condition' service-life, resulting in unequalled reliability, increased readiness and cost effectiveness. They are supplied both as individual couplings and as complete driveshafts.
The KAflex driveshaft had been fitted in accordance with Kamatics Corporation supplemental type certificate (STC) SH 7767SW. The helicopter was then ground run and test flown with no defects found. While the KAflex driveshaft remained fitted to the helicopter, the requirements of airworthiness directive (AD)/Bell 206/79 Amdt 14 were no longer applicable to the helicopter.
The STC documentation stipulated that, upon completion of the modifications and installation of the shaft, the historical service record was to be completed, applicable logbook entries made and the card to be kept with the aircraft logbooks. At the completion of its recommended time in service between overhauls, the shaft and the completed historical service card would be returned to the manufacturer for overhaul. While an entry in the helicopter's logbook was made for the installation of the KAflex shaft into the helicopter, no historical service record was found in the helicopter's logbooks pertaining to the shaft.
Maintenance and inspection
A copy of the STC was kept with the archived helicopter logbooks and worksheets, in a separate binder to the current helicopter logbook binder. Both binders were located at the operator's main office. The STC was available to the engineers maintaining the helicopter, but it was not identified by them as a document that they would need to refer to routinely in their maintenance activities.
Although the STC and the manufacturer's website stated that the driveshaft was 'maintenance free' Sections 3 and 4 of the STC detailed the inspection and maintenance regime that the manufacturer expected to be performed while the driveshaft was in service. Section 3 of the STC detailed pre-flight, 100-hourly and 1,500-hourly inspections that were to be performed throughout the 6,000 hour service life5 of the shaft. The inspection advice described examination of the flex frames for the production of 'red dust' showing up as a red metallic residue. Section 3 also contained requirements for a 6,000 hour inspection (which it referred to as maintenance requiring return to the manufacturer) and conditional inspections after specific events, such as an overtorque, an overspeed, a sudden stoppage, a hard landing or a lightning strike. Section 3 also contained the following bold type warning with regard to flex frame attachment hardware:
WARNING
DO NOT disturb or tighten flex frame nuts or bolts. Evidence of turning
fasteners by wrench or other means is cause for rejection.
Section 4 of the STC listed maintenance requirements for the driveshaft. That information stated that there was no periodic maintenance requirement for the KAflex driveshaft.
The operator's managing director stated that at no time did any of his personnel detect the production of red dust residue on the shaft. He also advised that had there been red dust production around the flex frame joints, his personnel would have detected it and prevented the failure. The manufacturer stated that red dust is usually produced in the initial stage of loss of integrity of the bolted joints, but noted that this was not always the case and operators should be vigilant with regard to inspection for loose bolted joints.
From the time of installation of the shaft on 19 January 1998 to the time of the occurrence on 14 June 2004, there were no entries detailing the conduct of periodic or 1,500-hourly inspection certification requirements of the KAflex driveshaft in the helicopter's logbooks, or in the worksheets for maintenance for the issue of a maintenance release. This represented the 4,112.35 hours in service for the KAflex driveshaft. However, there was no stipulation in the STC Section 3 instructions to require certification for the completion of the inspections detailed in that section.
There was also no amendment insert in the helicopter's flight manual for the daily inspection as described in the STC, Section 3 - DAILY INSPECTION BEFORE FIRST FLIGHT OF THE DAY. There was also no stipulation in the STC that the flight manual should be amended in order to make that information readily available to the pilot.
When interviewed, the pilot in command was asked to describe the execution of a daily inspection of the helicopter. While a detailed explanation was given to the interviewer, at no time was the driveshaft manufacturer's warning caveat mentioned or alluded to by the pilot. As this is a bold type warning in the manufacturer's documentation, it should have been a recall item readily identified during this discourse.
Historical service record
There was minimal reference made to the historical service record in the STC. A copy of the card was obtained from the local Australian distributor for KAflex. There was no provision on the card for certification of the 100-hourly and 1,500-hourly inspections. The historical service record card had not been incorporated into the maintenance records for the helicopter as required by the manufacturer in the accomplishment instructions of the STC.
1 International radio broadcast for urgent assistance.
2 A proprietary name for a driveshaft manufactured by a Unites States company, Kamatics Corporation.
3 Output shaft speed at 100% main rotor RPM.
4 AD/Bell 206/79 Amdt 1 detailed the inspection and installation of a Visual Aid Overheat Indicator on a Bell manufactured main input drive shaft assembly. It was later cancelled as those requirements were incorporated into the 100-hourly maintenance servicing requirements.
5 At the time of shaft installation, the STC stipulated a 4,000 hour service life. Service Instruction 2348 Revision "E" dated September 1999 extended this service life to 6,000 hours between overhauls.